Introduction

Background
Client Profile:
The client, a key player in the Canadian manufacturing sector, faced escalating costs due to inefficiencies in their production processes. Inadequate cost controls further exacerbated the challenge, threatening the company’s financial stability and competitiveness.
Challenges Faced:
1. Cost Overruns:
Inefficient production processes led to significant cost overruns, impacting the company’s profit margins and competitiveness in the market.
2. Inadequate Cost Controls:
The absence of robust cost control measures resulted in a lack of visibility and control over operational expenses, exacerbating the financial challenges faced by the manufacturing company.
Dexovise Analytics' FP&A Solution:
1. Comprehensive Cost Analysis:
Dexovise conducted a detailed cost analysis, examining each stage of the production process. This involved identifying cost drivers, analyzing production workflows, and assessing the efficiency of resource utilization.
2. Strategic Cost Control Measures:
Based on the findings from the cost analysis, Dexovise recommended and implemented strategic cost control measures. This included optimizing resource allocation, renegotiating supplier contracts, and identifying opportunities for cost savings without compromising product quality.
3. Streamlining Operations:
Dexovise collaborated with the client to streamline production operations. This involved reevaluating workflow processes, improving production scheduling, and implementing efficiency-enhancing technologies where applicable.
4. Performance Metrics Implementation:
To monitor the effectiveness of the implemented measures, Dexovise introduced performance metrics tailored to the manufacturing sector. This allowed for continuous monitoring and adjustment of strategies based on real-time data.
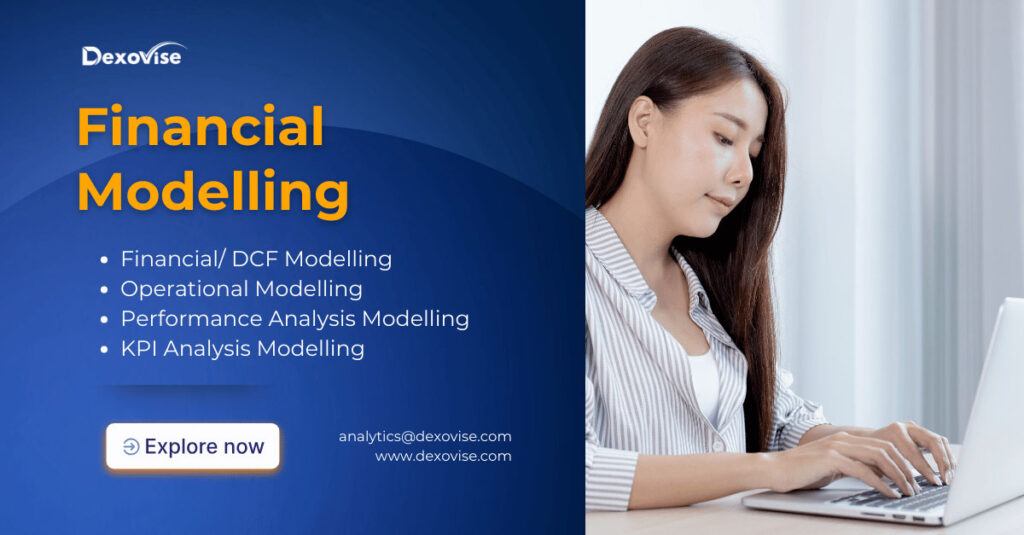
Results and Achievements:
Significant Cost Savings:
The comprehensive cost analysis and strategic cost control measures resulted in significant cost savings for the manufacturing company. This included reduced production costs, overhead expenses, and overall operational expenditures.
Improved Operational Efficiency:
Streamlining operations led to improved overall operational efficiency. The manufacturing processes became more streamlined, reducing lead times and enhancing the company’s ability to meet market demand promptly.
Enhanced Profit Margins:
The combination of cost savings and operational efficiency improvements contributed to enhanced profit margins. The manufacturing company experienced improved financial performance and strengthened competitiveness in the market.
Sustainable Cost Control:
Dexovise’s implementation of performance metrics enabled the manufacturing company to sustain cost control measures over the long term. Continuous monitoring and data-driven decision-making ensured ongoing operational efficiency.
Technology Trends in FP&A: Leveraging Innovation for Better Insights
Imagine a world where financial planning and analysis (FP&A) isn’t just about crunching numbers, but about unlocking game-changing insights that propel your business forward. 🚀
Key Learnings:
1. Comprehensive Analysis is Crucial:
Conducting a thorough cost analysis is essential to identify inefficiencies and cost drivers in the production process.
2. Strategic Cost Control is Effective:
Implementing strategic cost control measures, such as renegotiating contracts and optimizing resource allocation, can result in significant cost savings.
3. Streamlining Operations Enhances Efficiency:
Streamlining production operations improves overall efficiency, reduces lead times, and enhances the company’s ability to meet market demand promptly.
4. Performance Metrics Drive Sustainability:
Introducing performance metrics enables continuous monitoring and sustains cost control measures over the long term.
5. Data-Driven Decision-Making is Key:
Leveraging real-time data for decision-making ensures that strategies are continually adjusted based on accurate and up-to-date information.
6. Enhanced Profit Margins Contribute to Financial Health:
Improved operational efficiency and cost savings contribute to enhanced profit margins, strengthening the financial health of the company.
7. Continuous Monitoring is Essential:
Continuous monitoring of performance metrics ensures ongoing operational efficiency and allows for timely adjustments to strategies.
8. Operational Streamlining Supports Market Competitiveness:
Streamlining operations not only improves efficiency but also enhances the company’s competitiveness in the market.
9. Adaptability is a Key Factor:
The ability to adapt and optimize operations based on insights gained from the cost analysis and performance metrics is critical for sustained success.
10. Collaboration with FP&A Experts Drives Positive Outcomes:
Partnering with FP&A experts, like Dexovise Analytics, brings valuable insights and strategic guidance, leading to positive outcomes in addressing operational challenges.
Conclusion
Dexovise Analytics’ collaboration with the Canadian manufacturing company exemplifies the transformative impact of strategic FP&A services in revitalizing operational efficiency. By addressing cost overruns and implementing targeted cost control measures, Dexovise not only stabilized the company’s financial health but also positioned them for sustainable growth in the competitive manufacturing sector. This case study serves as a testament to Dexovise’s ability to drive positive outcomes in the face of complex operational challenges.